What is Acrylic?
Table of Contents
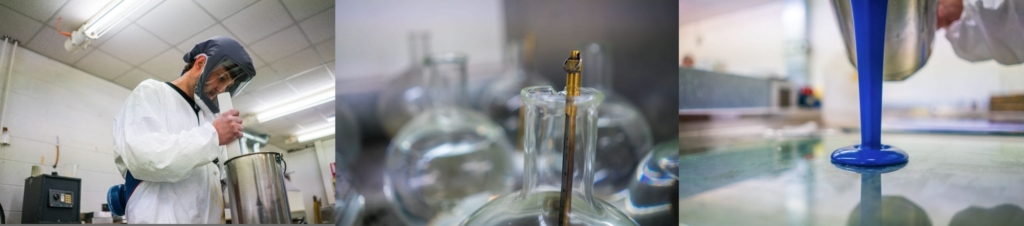
Origins of acrylic
A synthetic resin, acrylic is produced from the polymerisation of methyl methacrylate. Poly(methyl methacrylate), also known as acrylic, is a transparent thermoplastic – often used in sheet form as a lightweight or shatter-resistant alternative to glass. Acrylic is often sold in sheet form under brands such as Altuglas, Plexiglass, Perspex, and Lucite. As an acrylic manufacturer, here at Midton we work with both sheet acrylic and cast acrylic, for acrylic encapsulation.
Like all plastics, acrylics are polymers. The word, polymer, derives from the Greek word poly, meaning many, and meros, meaning a part. Thus, a polymer is a material made up of many molecules, linked in a chain. These polymers may have hundreds, or thousands, of molecules linked together. Additionally, these polymers have properties entirely different from its individual component parts.
The first acrylic acid was created in 1843, with methacrylic acid following closely behind, formulated in 1865. Acrylic was a British discovery, found in the early 1930s by chemists Rowland Hill and John Crawford at Imperial Chemical Industries (ICI) in England. ICI registered the product under the trademark Perspex. Around this time, chemist and industrialist Otto Röhm of Rohm and Haas AG in Germany attempted to produce safety glass by polymerising methyl methacrylate between two layers of glass. The polymer separated from the glass as a clear plastic sheet, which Röhm gave the trademarked name Plexiglass. Both Perspex and Plexiglass were commercialised in the late 1930s.
Following this, Dupont, in the United States, subsequently introduced their own product under the trademark Lucite. The first major application of the new plastic took place during World War II, when acrylic was made into aircraft windows and bubble canopies for gun turrets. Civilian applications of PMMA followed after the war, and are now an integral part of today’s society.
What is it made of?
Polymethyl methacrylate as a polymer, derives from the basic molecule (or monomer) methyl methacrylate ([CH2=C(CH3)COOCH3]). Methyl methacrylate may be formed in several ways. A common way is to react acetone [CH3COCH3] with hydrogen cyanide [HCN] to produce acetone cyanohydrin [(CH3)2C(OH)CN]. This, in turn, is a reaction with methyl alcohol to produce methyl methacrylate.
PMMA is produced by free-radical polymerisation of methyl methacrylate in mass or suspension polymerisation. During polymerisation, one leg of this double bond breaks and links up with the middle carbon atom of another methyl methacrylate molecule to start a chain. This process continues to repeat itself until the final polymer is formed. Controlling the proportion of these monomers produces changes in elasticity and other properties in the resulting plastic.
Properties of acrylic
A clear, colourless polymer, acrylic is available in pellet, small granules, and sheet form – which go on to be formed through all thermoplastic methods. Acrylic is suitable for processing by injection molding, casting, extrusion and thermoforming. Additionally, the material is a thermoplastic, which addresses the way it responds to heat.
Thermoplastics become liquid at their melting point (160 degrees Celsius in the case of acrylic). This means that they can essentially be heated, cooled, and reheated without significant damage. Instead of burning, thermoplastics liquify, allowing molding and recycling. Due to this, PMMA is endlessly recyclable, making it a sustainable plastic. In contrast, thermoset plastics, such as resin, can only be heated once. This first heating causes thermoset materials to set, causing a chemical reaction that cannot be reversed. If you attempt to reheat a thermoset plastic, it will burn. This makes thermoset materials a poor candidate for recycling.
Acrylic is a tough, highly transparent material that can be coloured, moulded, cut, drilled, and formed. In terms of properties, acrylic exhibits glass-like qualities such as brilliance, clarity, and transparency. The plastic has 10 times the impact resistance of glass, with half the weight.
Commonly used throughout society, acrylic is used throughout architecture and construction, lighting, design, automotives, electronics, and medical supplies. As an bespoke manufacturer, we’re here to help with any project you may have in mind.
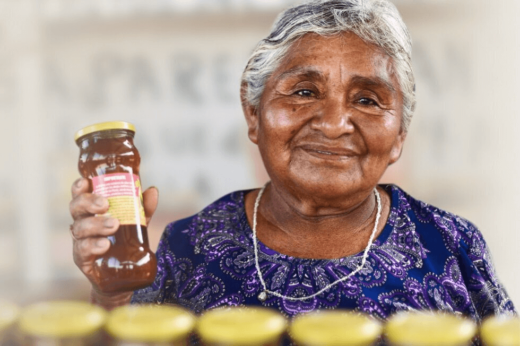
Lendwithcare and Midton
Here at Midton, we are dedicated to continuously improving our efforts when it comes to ecological…
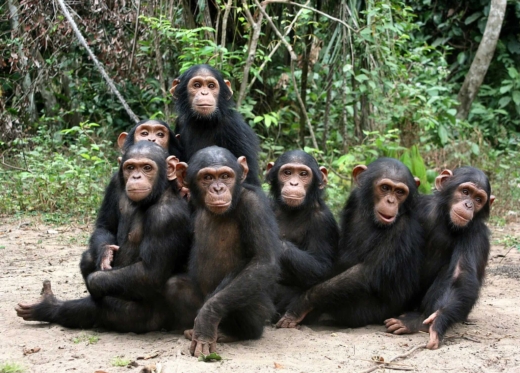
One Tree Planted: Uganda 2022
March has been a fantastic month for us here at Midton, seeing our highest value of sales in three years.…
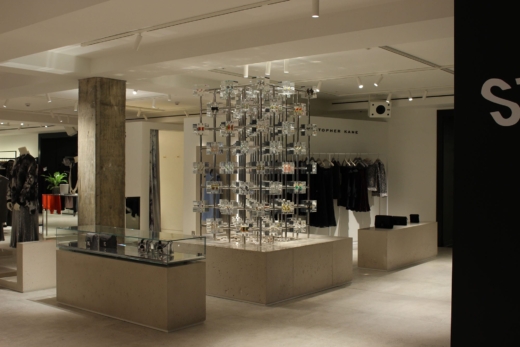
Choosing an Acrylic Display Case
An acrylic case would make the perfect addition to any shop displays and office environments.…